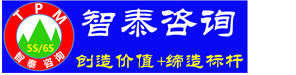
智泰咨询公司(TPM咨询公司)认为企业在工厂维护活动中开始运用TPM管理概念,整个工作团队必须首先确定高层管理负责此项目。第一步是雇用或指派一个TPM专员,TPM专员的职责是通过一个教育课程将TPM管理概念灌输给团队成员。
教育使员工相信TPM咨询管理不是一个“月度项目”,而是长期推进的管理项目。一旦专员确信员工己接受TPM管理体系并了解它及所涉及的事宜,第一学习行动小组就组建了。这些团队通常由对问题阐述有直接影响的人员构成,操作工,维护人员、当班主管、计划员、高层管理人员都可能加入团队。每个人都成为此过程的“股东”并被鼓励尽其所能为团队的成果作出贡献。
通常,TPM专员带领全队,直到其他人对程序熟悉并且自然诞生团队领袖。行动组负责确定问题区域,细化纠正措施并开创纠正程序。认识问题和想出解决方案对一些队员来说并不容易。他们没有其他工厂的工作经验以及在那里有机会看到处理事情的不同方法。TPM运作良好的工厂,队员经常参观一些合作工厂以积累和比较TPM的方法、技巧和进展工作。
这个比较过程是一个全面测量技巧的一部分,称作“基准”,是TPM管理大的财富之一。鼓励团队从小问题开始工作并对进展严密记录。管理层总是认可团队早期工作的成功完成。程序的公开化和结果是使项目成功的秘密之一,一旦团队熟悉了TPM管理并有了小问题成功解决的经验方法后,再提出一些更重要和复杂的问题,例如,一个制造工厂选择了钻孔压力机作为一个问题领域,团队将机器研究和评估得极细致,使用延时生产来建立一个生产时间与非生产性时间相比较的记录。一些队员参观了亚洲以外的一个工厂,他们有类似的压力机并运行,高效得多,这次参观使他们有了如何改进现状的主意。
将机器带入“世界级’生产条件的措施很快被设计出来并启动工作。工作包括停机清洁、油漆、调整、更换坏损的零件、传送带、软管等。作为程序的一部分,回顾操作和机器维护的培训。开发一个由操作工完成的维护职责日常检查,在一台机器获得成功后,记录开始展现程序提高了多少生产量,就可选择另一台机器,然后再一台,直到整个生产区域都进入“世界级’条件并以显著更高的速度进行生产。
注意在以上方面需要操作工积极的参与机器的维护。这是TPM的基础创新之一。“我是操作它”的态度不再被接受。日常维护检查,较小的调整、润滑和小部分改变都成为操作工的职责。在操作工协作下,工厂维护人员处理多方面的彻底检查和重大的故障。即使召集了外部维护和工厂的专家,设备操作工也应该在修理过程中扮演一个重要的角色。TPM使用的主要手段名为设备综合效率(OEE),这个数字与六大损失相关联:
1.故障/停机损失(EquipmentFailure/BreakdownLosses)
2.换装和调试损失(SetupandAdjustment)
3.空闲和暂停损失(IdlingandMinorStoppageLosses)
4.减速损失(ReducedSpeedLosses)
5.质量缺陷和返工(QualityDefectsandRework)
6.启动损失(StartupLosses)
三个可测量的:可用(时间)、完成(速度)和产出/(质量)
当来自时间,速度,质量的损失被综合在一起,最终OEE数字反映出任何设备或生产线的运行状况。
TPM被鼓励用来设定OEE目标和来自这些目标的测量偏差,然后问题解决组试图来消减差异,加强业绩。
深圳市智泰企业管理咨询有限公司是全国领先的咨询机构,智泰咨询专注于企业的TPM管理,5S管理、6S管理、精益生产、精益品质、精益成本、精益班组等领域的咨询指导。